HENAN YUMO: Engineered Precision, Uncompromised Performance
Brown Fused Alumina: Properties, Applications, and Advantages in Industrial Abrasives.
Discover why this cost-effective, high-toughness abrasive dominates heavy-duty grinding, surface preparation, and refractory industries.
5/20/20252 min read
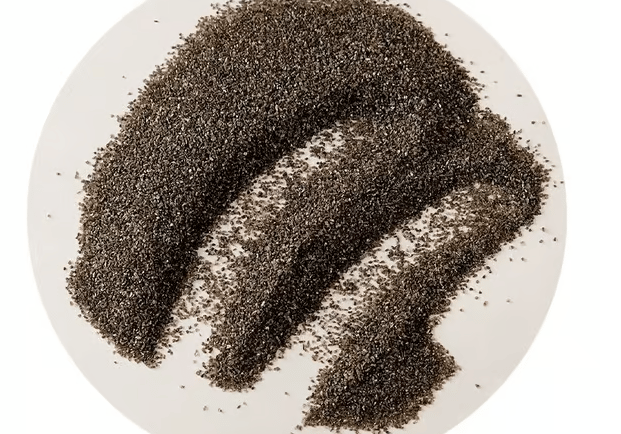
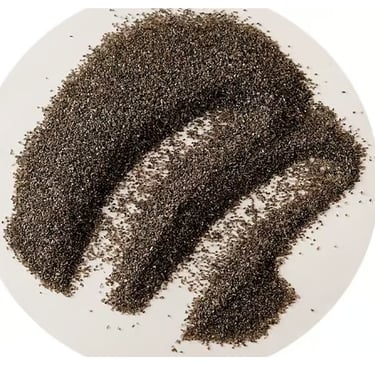
Introduction to Brown Fused Alumina (BFA)
Brown Fused Alumina (BFA), composed of 94–97% aluminum oxide (Al₂O₃), is a robust synthetic abrasive produced by smelting bauxite in electric arc furnaces at 2000–2200°C. Its unique combination of hardness (Mohs 8.8), toughness, and thermal resistance makes it a go-to solution for demanding industrial applications, from metalworking to refractory linings.
Key Properties of Brown Fused Alumina
Chemical Composition:
Al₂O₃: 94–97% (primary component).
TiO₂: 1.5–3.5% (enhances toughness).
SiO₂: ≤1.2%, Fe₂O₃: ≤0.5% (low impurities).
Physical Characteristics:
Hardness: Mohs 8.8, balancing cutting efficiency and durability.
Density: 3.9–4.0 g/cm³ (ideal for bonded abrasives).
Thermal Stability: Withstands temperatures up to 1850°C.
Grain Structure:
Angular, blocky crystals for aggressive material removal.
Lower friability than white fused alumina, ensuring longer tool life.
Top Industrial Applications of Brown Fused Alumina
1. Heavy-Duty Grinding & Metalworking
Applications:
Cast Iron Grinding: BFA F24–F60 grit removes burrs and surface defects efficiently (MRR ≥25 cm³/min).
Steel Plate De-scaling: Blasting with BFA F16–F30 grit achieves Sa 2.5 cleanliness.
Benefits:
20% lower tool wear vs. silicon carbide in steel processing.
Cost-effective for large-scale operations.
2. Refractory Materials & Foundry
Applications:
Furnace Linings: BFA aggregates (1–5 mm) resist slag corrosion in steel ladles.
Mold Coatings: BFA powder reduces sticking in iron casting molds.
Benefits:
Thermal shock cycles: 50+ cycles without cracking.
Reduces refractory replacement costs by 15–20%.
3. Surface Preparation & Sandblasting
Applications:
Shipyard Rust Removal: BFA F16–F40 grit cleans hulls 30% faster than garnet.
Concrete Profiling: Prepares surfaces for coatings with CSP 3–5 profiles.
Benefits:
Recyclable up to 5 times, minimizing waste.
Lower dust generation vs. coal slag.
4. Bonded Abrasive Tools
Applications:
Cutting Wheels: BFA grains in resin bonds for steel rebar cutting.
Grinding Discs: Vitrified bonds for angle grinders (e.g., weld seam smoothing).
Benefits:
Higher bond retention than white fused alumina.
Compliant with OSHA silica exposure limits.
Case Study: BFA in Automotive Brake Drum Manufacturing
Challenge: A manufacturer needed to reduce grinding time for cast iron brake drums while maintaining Ra ≤3.2μm.
Solution: Yumo’s BFA F36 grit with vitrified grinding wheels.
Results:
Cycle time reduced from 8.5 to 6.2 minutes per drum.
Surface roughness improved to Ra 2.8μm.
Annual abrasive costs lowered by $18,000.
How to Select the Right Brown Fused Alumina
Grit Size Guidelines:
Coarse (F12–F40): Heavy material removal, sandblasting.
Medium (F46–F120): Surface finishing, tool sharpening.
Fine (F150–F220): Final polishing of castings.
Packaging Options:
Bulk (1-ton bags) for foundries.
25kg moisture-resistant bags for workshops.
Quality Certifications:
Ensure compliance with FEPA 42-1:2006 and ISO 8486-1:2023.
FAQs About Brown Fused Alumina
Q: Is BFA environmentally friendly?
A: Yes. BFA is non-toxic and recyclable. Yumo’s production adheres to REACH and RoHS standards.
Q: Why choose BFA over white fused alumina?
A: BFA offers better cost efficiency for heavy grinding, while WFA excels in precision tasks.
Q: What’s the lead time for custom grit sizes?
A: Yumo delivers tailored BFA grits within 7–10 business days (MOQ: 500kg).