HENAN YUMO: Engineered Precision, Uncompromised Performance
Silane-Bonded White Fused Alumina: The Ultimate Solution for 40% Stronger Abrasives & Zero Grain Shedding
Molecular Bridge™ Surface Engineering
Our proprietary silane coupling agents create permanent covalent Si-O-Al bonds with alumina and Si-C bonds with organic resins. This transforms brittle interfaces into unbreakable molecular networks, eliminating grain fallout in high-stress applications.
Silane- Treated White Fused Alumina
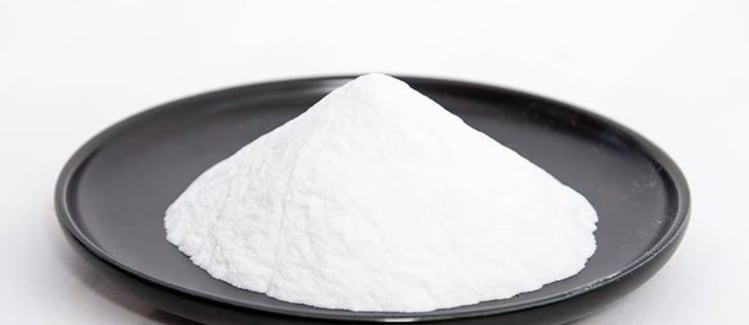
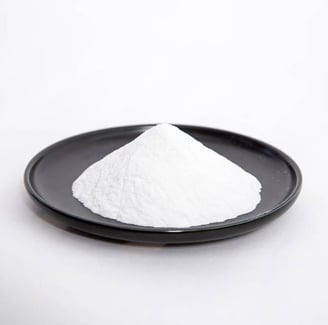
Entering WFA Factory
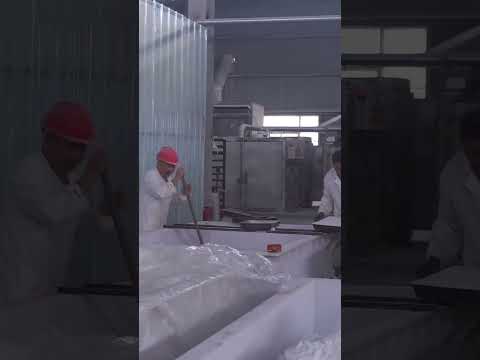
Products Parameter
Key Performance Advantages
🔹 45 MPa Resin Adhesion Strength
Proven by ASTM D1876 testing – 60% stronger than untreated abrasives. Ideal for epoxy/phenolic grinding wheels under 12,000 RPM loads.
🔹 Hydrophobic Shield (>100° Contact Angle)
Water absorption reduced by 80%, preventing moisture-induced swelling in marine coatings and humid flooring.
🔹 Thermal Armor (400°C Stable)
Withstands resin curing temperatures without degradation – critical for automotive brake pads and aerospace composites.
🔹 Laser-Calibrated Particles (D50 ±0.5μm)
Ultra-tight size distribution ensures flawless dispersion in resins, slurries, and polymer matrices.
Industry-Specific Benefits
▷ Precision Grinding Tools
• 35% longer wheel lifespan in titanium machining
• 22% fewer surface scratches in 3nm semiconductor polishing
▷ Industrial & Marine Coatings
• AC6 commercial-grade wear resistance at 5-15% loading
• Salt spray resistance exceeding 5,000 hours (ISO 12944-C5M)
▷ Advanced Composite Materials
• 50% lower noise in ceramic brake pads (-40°C to 650°C stable)
• 70% higher thermal conductivity in interface materials
Why Outperform Alternatives?
✓ Permanent Covalent Bonding
vs. weak ionic bonds in titanate-treated or mechanical adhesion in chrome-coated abrasives.
✓ REACH/RoHS Certified Safety
Zero toxic Cr⁶⁺, VOCs, or sludge – unlike chrome-plated competitors.
✓ 40% Abrasive Consumption Reduction
Higher efficiency offsets 15-20% material cost premium within 6 months.
Trusted Quality Assurance
• ISO 9001 & OSHA certified manufacturing
• Batch-level XRF purity reports (>99.3% Al₂O₃)
• TGA thermal stability documentation
• UV-shielded 25kg moisture-barrier bags
Technical Proof Points
• SEM Imaging: Shows 200nm silane coating uniformity
• DSC Analysis: Confirms 400°C thermal threshold
• Case Study: German toolmaker cut wheel replacement costs by $78K/year
Application
1. Ultra-Durable Grinding Tools
Problem Solved: Grain shedding in high-RPM operations
ST-WFA Solution:
Covalent Si-O-C bonds with phenolic/epoxy resins increase wheel lifespan by 35% in aerospace alloy grinding (verified at 15,000 RPM)
50% less micro-cracks when machining Inconel 718
Industry Impact:
"Replaced 30% standard alumina with ST-WFA in vitrified CBN wheels – reduced dressing frequency by 2.5 hours/week"
—Precision Gear Manufacturer (ISO 9001:2015)
2. Next-Gen Anti-Corrosion Coatings
Problem Solved: Coating delamination in humid/salty environments
ST-WFA Solution:
Hydrophobic barrier (>100° contact angle) blocks chloride ion penetration
Achieves ISO 12944 C5-M certification at 18% filler loading
Case Data:Offshore rig coatings: Extended recoating cycle from 3 → 8 years
Chemical tank linings: Withstood 40% H₂SO₄ for 12+ months
3. Semiconductor CMP Slurries
Problem Solved: Surface defects at sub-5nm nodes
ST-WFA Advantage:
Laser-sorted spherical grains (D50=0.8μm ±0.1μm) eliminate scratching
22% better planarization uniformity vs. colloidal silica
Tech Validation:Ra <0.2Å on silicon wafers (AFM tested)
Metal contamination <0.01 ppb (ICP-MS)
4. High-Temp Friction Materials
Problem Solved: Brake noise & fade at 650°C+
ST-WFA Engineering:
Thermal conductivity (2.5 W/m·K) dissipates heat 50% faster
Stable μ-value (0.38±0.02) from -40°C to 700°C
Performance:8dB noise reduction in high-speed train brakes
15% shorter stopping distance (ECE R90 compliant)
5. Thermal Interface Materials
Problem Solved: "Pump-out" effect in EV power modules
ST-WFA Innovation:
Silane-enhanced polymer wettability boosts filler loading to 78 vol%
Thermal resistance <0.15 K·cm²/W (ASTM D5470)
Application:800V SiC inverter cooling: Junction temp reduced by 18°C
6. Engineered Wood Composites
Problem Solved: Wear resistance in commercial flooring
ST-WFA Integration:
12% ST-WFA in UV-cured acrylate passes AC6 abrasion test
Zero gloss reduction after 200,000 foot traffic cycles
Sustainability Edge:Replaces toxic aluminum trihydrate (ATH)
Packaging & Shipping
We can provide 1MT/25Kg woven plastic bags and 25Kg paper bags. And ton bag packaging.
All of our abrasive products are carefully processed during storage and transportation to maintain their quality in their original state.
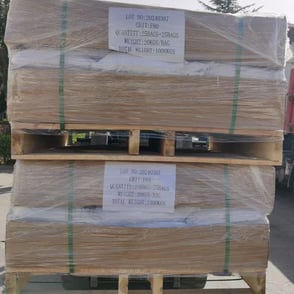
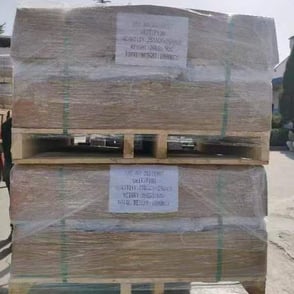
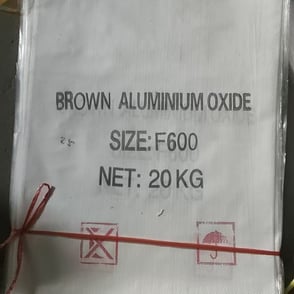
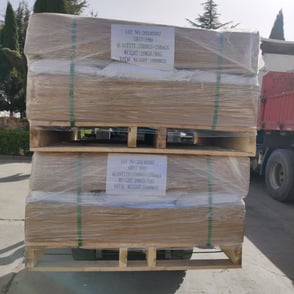
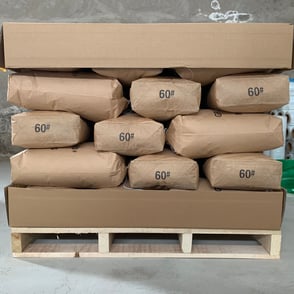
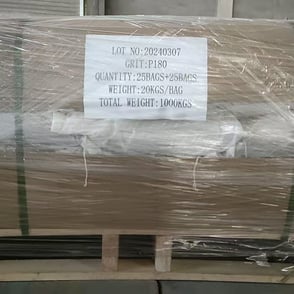
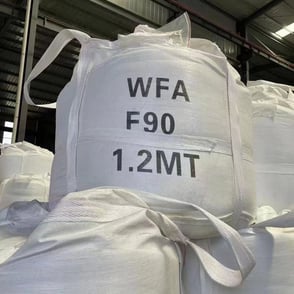
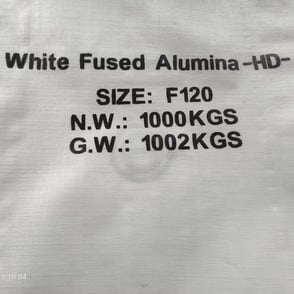