HENAN YUMO: Engineered Precision, Uncompromised Performance
Refractory Castables: Why White Alumina Wins
White fused alumina (WA) stands at the forefront of refractory castable innovation. As industries worldwide demand higher operational temperatures, stricter environmental controls, and enhanced chemical resistance, WA’s exceptional properties make it the undisputed choice for engineers prioritizing reliability, longevity, and peak performance. This isn’t just material science—it’s industrial resilience redefined.
7/2/20253 min read
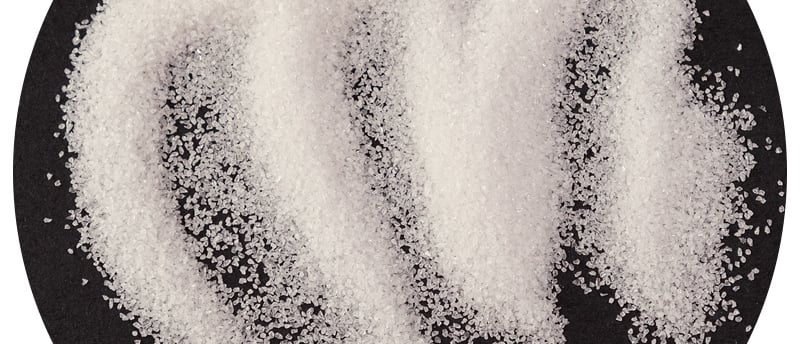
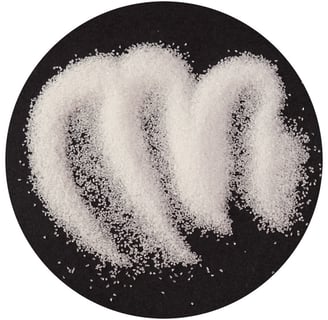
Refractory Castables: Why White Alumina Wins
The Unmatched Value of White Fused Alumina in Modern Industrial Solutions
White fused alumina (WA) stands at the forefront of refractory castable innovation. As industries worldwide demand higher operational temperatures, stricter environmental controls, and enhanced chemical resistance, WA’s exceptional properties make it the undisputed choice for engineers prioritizing reliability, longevity, and peak performance. This isn’t just material science—it’s industrial resilience redefined.
1. Core Properties: The Scientific Edge of White Alumina
Synthesized by fusing >98.5% pure industrial alumina in electric arc furnaces exceeding 2000°C, white fused alumina undergoes crushing and magnetic purification to achieve its signature characteristics:
Extreme Hardness & Wear Resistance: With a Mohs hardness of 9.0, WA outperforms brown fused alumina and rivals silicon carbide in abrasion resistance, significantly reducing erosion in slag-rich environments.
Chemical Inertness: Minimal reactive impurities (SiO₂/Fe₂O₃ <0.5%) grant exceptional resistance to acidic/alkaline slags, molten metals, and corrosive gases—critical in glass furnaces and chemical reactors.
Thermal Stability: WA maintains structural integrity up to 1900°C, resisting sintering shrinkage and microcracking thanks to its low thermal expansion coefficient (7–8×10⁻⁶/K).
Engineered Particle Morphology: Spherical grains optimize packing density in castables, while angular variants enhance mechanical anchoring.
These properties establish WA as the structural backbone of high-performance refractory systems.
2. How White Alumina Transforms Castable Performance
2.1 Superior Thermo-Mechanical Resilience
WA-reinforced castables retain over 70% of cold crushing strength after thermal cycling—far exceeding the <50% retention of conventional high-alumina compositions. This is vital for furnaces undergoing daily thermal shocks. In standardized water-quench tests, WA-spinel formulations withstand 30+ cycles without spalling, doubling the endurance of bauxite-based alternatives.
2.2 Microstructural Mastery
Pore Architecture: WA’s uniform particle distribution creates submicron pores when bonded with microsilica or hydratable alumina. This dual-action microstructure blocks slag penetration while allowing steam escape during drying—preventing explosive spalling.
Reactive Synergy: WA reacts with MgO to form in-situ spinel (MgAl₂O₄), generating controlled 5% expansion that seals matrix gaps during service. Pre-formed spinel systems avoid expansion but compromise corrosion resistance.
2.3 Corrosion Defense Mechanisms
In glass tank regenerators, WA-rich castables form a protective viscous layer when attacked by soda-lime slag, dramatically slowing dissolution. When enhanced with zirconia (AZ castables), liner lifespan increases by 40%. WA’s purity also enables cleaner binder decomposition—systems using hydratable magnesium carboxylate achieve 200% higher gas permeability than cement-bonded alternatives, preventing pressure-induced failures.
3. Why White Alumina Outperforms Alternatives
While cost-driven alternatives exist, WA delivers unmatched ROI in critical applications:
Brown Fused Alumina: Contains 3–5% Fe₂O₃/TiO₂, accelerating slag corrosion. WA’s >98.5% purity provides superior defense.
Silicon Carbide (SiC): Oxidizes above 1400°C, forming weakening gaseous byproducts. WA remains stable to 1900°C with no strength degradation.
Low-Grade Aggregates: Form unstable glassy phases at high temperatures. WA maintains crystalline integrity under load (refractoriness under load >1700°C).
4. Industrial Applications: Where White Alumina Dominates
4.1 Metals Processing
Steel Ladles: WA-MgO castables withstand basic slags for 120+ heats—50% longer than high-alumina linings.
Aluminum Transfer: WA’s non-wettability minimizes metal buildup in launders and tundishes.
4.2 Glass Manufacturing
Forehearths: WA-mullite-zirconia (AMZ) compositions resist siliceous glass corrosion at 1500°C.
Regenerator Checkers: WA prevents structural sagging under thermal cycling in aggressive flue-gas environments.
4.3 Petrochemical & Energy
Reformer Furnaces: Chrome-free WA castables resist catalytic coke formation in hydrocarbon cracking.
Solar Thermal: WA-insulating castables line CSP receivers enduring >1000°C cyclic operation.
5. Innovations Driving WA’s Future
5.1 Advanced Processing Breakthroughs
Microwave Sintering: WA-ZnO castables achieve 95% density in minutes (vs. hours) with 70% energy savings, while forming homogeneous ZnAl₂O₄ spinel for enhanced strength.
Nano-Seeding: Adding 1–2% α-Al₂O₃ nanoparticles lowers spinel formation temperature by 150°C, improving densification.
5.2 Sustainable Engineering
Low-Cement Castables (LCC): WA’s reactivity enables cement reductions to 3–5%, slashing CO₂ emissions by 30% and water usage by 25%.
Closed-Loop Recycling: Companies like Henan Yumo reprocess spent WA castables into secondary linings, reducing virgin material consumption by 40%.
6. Strategic Sourcing: Maximizing WA’s Potential
Material consistency dictates castable performance. Key considerations:
Chemical Uniformity: Henan Yumo guarantees <0.1% batch-to-batch Al₂O₃ variance—critical for predictable thermomechanical behavior.
Application-Tailored Grading: From slag-line aggregates (1–3mm) to ultrafine powders (d₅₀=1.5µm) for low-porosity gunning mixes.
Technical Collaboration: Joint optimization of parameters like WA gradation or spinel ratios ensures peak performance in vibratable, self-flow, or shotcreting applications.
Conclusion: Engineering Certainty in Extreme Environments
White fused alumina transcends commodity status—it’s the foundation of next-generation refractory engineering. By extending furnace campaigns 30–60%, enabling thinner energy-efficient linings, and resisting the most corrosive industrial environments, WA proves indispensable for sustainable high-temperature processing.